Imágenes térmicas para mantenimiento preventivo en turbinas eólicas
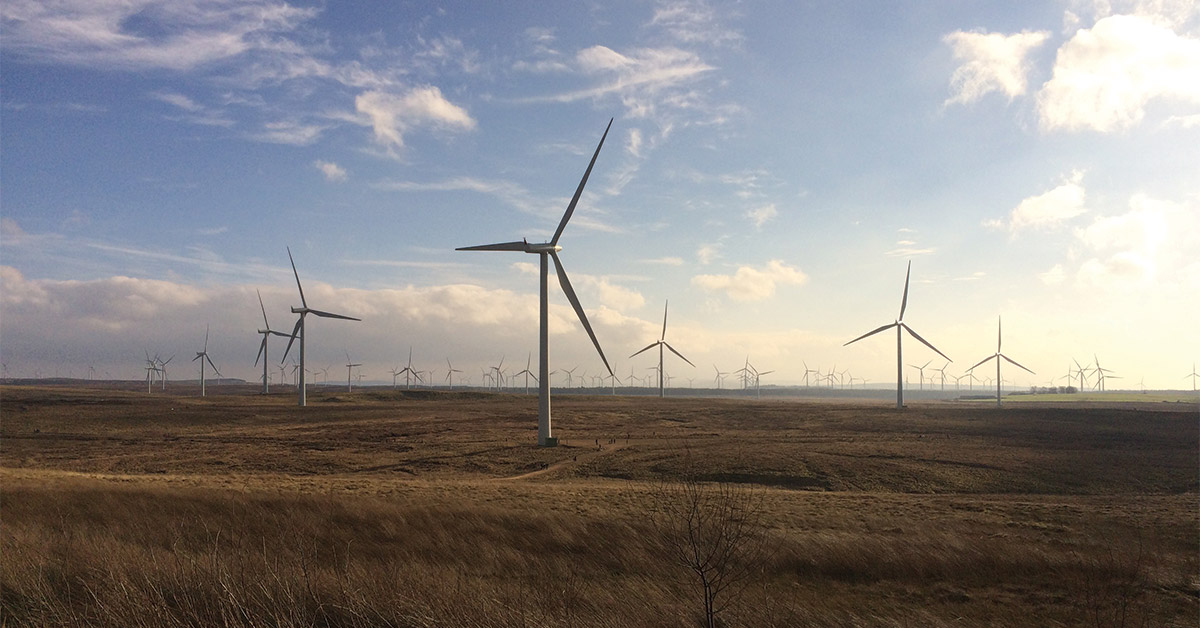
A medida que los parques eólicos envejecen y se quedan sin garantía, aumenta la importancia de realizar mantenimiento preventivo para los propietarios y operadores. Al detectar fallos inminentes de componentes, los operadores pueden evitar costosos fallos y tiempos de inactividad. La obtención de imágenes térmicas puede ayudar a detectar estos fallos de un vistazo, incluso durante el funcionamiento.
El viento ha sido una parte establecida de la generación de electricidad en Australia durante muchos años. Es una de las principales fuentes de energía renovable de Australia, que genera suficiente electricidad para satisfacer el 7,1 % de la demanda total de electricidad del país. A finales de 2018, había 94 parques eólicos en Australia, con casi 6 GW de capacidad de generación eólica.
El fuerte crecimiento de la capacidad de energía eólica en los últimos años ha provocado un fuerte aumento en el número de turbinas que han llegado al final del periodo de garantía del fabricante. Esto supone inevitablemente un riesgo financiero para el propietario para proporcionar funcionamiento y mantenimiento rentables.
Mantenimiento preventivo eficiente
El mantenimiento posterior a la garantía es esencial para mejorar la fiabilidad y la rentabilidad de la instalación de la turbina eólica. Con el fin de reducir los costes de mantenimiento y mejorar la rentabilidad, los operadores están cambiando cada vez más las actividades de mantenimiento reactivo a preventivo.
Los componentes de las turbinas eólicas son vulnerables al desgaste y pueden averiarse. Por eso son tan importantes el mantenimiento preventivo y las inspecciones periódicas. Por desgracia, los costes de mantenimiento pueden ser elevados, por lo que las inspecciones preventivas deben organizarse de la forma más eficiente posible. Los costes operativos y de mantenimiento pueden suponer fácilmente del 20 al 25 % del coste total por kWh producido durante la vida útil de la turbina eólica.
Cámaras termográficas
La termografía es la única tecnología que permite a los operadores inspeccionar todos los componentes mecánicos y eléctricos de las turbinas eólicas y del sistema eléctrico circundante. La regla general tanto para los componentes mecánicos como para los eléctricos es que se calientan antes de fallar. Las cámaras termográficas detectan ese aumento de la temperatura antes de que aparezca una avería. Los puntos calientes aparecen claramente en la termografía.
Una cámara térmica puede mostrar problemas en los engranajes y el motor, como desalineación de ejes, así como problemas eléctricos difíciles de ver como conexiones sueltas o desequilibrio de cargas. La versatilidad de las cámaras térmicas permite a los operadores de mantenimiento sacar el máximo partido al programa de mantenimiento preventivo.
Estuche: Cómo evitar posibles fallos de codos de ruptura muerta
Las terminaciones de codo de ruptura muerta se utilizan comúnmente en aplicaciones de parques eólicos y servicios públicos, en transformadores, cajas de conexiones e interruptores de aislamiento. Los fallos de este tipo de terminación pueden ser muy peligrosos y costosos con respecto a los daños del equipo adyacente y las interrupciones del servicio.
A continuación se muestra un ejemplo de una conexión fallida de ruptura muerta. En este caso, el componente dañado podría causar la pérdida de 25 MW de generación de energía durante aproximadamente 15 horas.
Anomalía del codo de ruptura muerta en un transformador de 1850 KVA
Los fallos de terminaciones pueden deberse a un montaje deficiente, la inexperiencia del instalador o el incumplimiento a rajatabla de las instrucciones. Las condiciones ambientales también pueden hacer que los materiales se expandan, contraigan o muevan, lo que a su vez puede conducir a un fallo de la terminación. Los cables pueden ser pesados debido al hielo que se acumula en el espacio muerto debajo de los gabinetes de terminación, lo que provoca tensiones en el cable. La helada de los equipos en los meses de invierno también puede cumplir un papel en el movimiento de los cables, lo que da lugar a un posible fallo.
Soportes utilizados para estabilizar conductores en un transformador de turbina eólica de 1850 KVA.
Cuando se visualizan con una cámara térmica, las anomalías en los codos de ruptura muerta se muestran claramente como pérdidas de calor.
Una anomalía detectada durante un escaneo IR rutinario en un transformador de turbina eólica de 1850 KVA
En los ejemplos siguientes, puede ver la diferencia de temperatura entre una terminación expuesta y una cubierta con un defecto. En la primera serie de pruebas, una terminación se dañó intencionadamente y se sometió a 100 amperios de corriente durante un período de 75 minutos. La segunda serie de imágenes ilustra la misma terminación con la funda protectora instalada para demostrar el patrón de calentamiento y el delta entre las dos áreas.
15 minutos en la prueba de 100 A. Conector desnudo 44,2 °C frente a protección blindada 26,9 °C - ΔT 17,3 °C
45 minutos en la prueba de 100 A. Conector desnudo 69,6 °C frente a protección blindada 35,7 °C - ΔT 33,9 °C
75 minutos en la prueba de 100 A. Conector desnudo 72,3 °C frente a protección blindada 40,9 °C - ΔT 38,4 °C
Estuche: Inspecciones de la pala de turbina
Las palas de los generadores de energía eólica se fabrican con materiales compuestos, son sólidas y ligeras. Sin embargo, están continuamente sometidas a importantes cantidades de tensión que pueden ocasionar grietas durante los procesos de fabricación y prueba. En el peor de los casos, las palas pueden incluso frenar durante el funcionamiento y soltarse del rotor, lo que puede provocar accidentes potencialmente mortales.
Con las cámaras de imagen térmica, es posible inspeccionar la pala mientras está en movimiento. Los defectos, como las grietas, alteran la firma térmica del material. De esta forma, los infrarrojos pueden detectar pequeños cambios en los compuestos de las palas de la turbina que, de otro modo, pasarían desapercibidos solo por la inspección visual.
La termografía puede detectar una variedad de anomalías, como roturas, defectos debidos a rayos, puntas dañadas y problemas de fibra. Las cámaras térmicas también detectan problemas de estanqueidad, falta de uniones adhesivas, errores de paso de pala y mucho más. La detección de estas anomalías en una etapa temprana, cuando son pequeñas, reducirá el coste y evitará daños graves.
Beneficios de la termografía
La termografía proporciona una visión general inmediata de la firma térmica de la turbina eólica, lo que permite a los operadores ver los defectos de un vistazo. Con una cámara térmica, las inspecciones pueden incluso realizarse desde el suelo, sin necesidad de subir a la torre.
La precisión es probablemente el principal motivo por el que los operadores de mantenimiento recurren a la termografía. Con una cámara térmica, no solo puede ver defectos en la superficie exterior de la pala, sino también más profundamente dentro de la pala. Por último, estos defectos internos son los que contribuyen a la falla si los problemas persisten.
La obtención de imágenes térmicas permite a los inspectores cubrir grandes áreas desde lejos. Al menos, esto reduce el número de comprobaciones físicas/visuales y acelera el trabajo de mantenimiento y hace que sea más rentable.
Cámaras FLIR para mantenimiento preventivo
La incorporación de tecnología termográfica en la rutina de inspección de mantenimiento preventivo permite a las empresas de parques eólicos supervisar el equipo en condiciones de funcionamiento cuando lo deseen. Añadir un termógrafo a la rutina de mantenimiento preventivo les ayudará a mejorar la eficiencia y maximizar la rentabilidad al detectar problemas eléctricos y mecánicos antes de que provoquen un costoso tiempo de inactividad no planificado.
Las anormalidades de temperatura se pueden localizar de forma eficiente utilizando un termógrafo de mano, como la cámara térmica FLIR T1040 HD. Esta cámara ofrece las imágenes más nítidas, las temperaturas más exactas y la mayor flexibilidad. La FLIR T1040 HD cuenta con una combinación única de MSX® (imagen dinámica multiespectral), tecnología de mejora de imagen UltraMax® y algoritmos de filtrado adaptativos, que permiten a los usuarios grabar las imágenes más fluidas y detalladas.